SAND & SAND ADDITIVES
Sand is the primary material to create molds and cores in the sand casting process, and sand additives are mixed with the sand to enhance its performance and the casting quality. Together, both of these materials make it possible to customize the sand's properties and meet the specific needs of different metals and casting methods.
The type of sand and additives directly influence the quality, dimensional accuracy, and surface finish of the casting.
Sand Options
SILICA SANDS
We stock a wide variety of sub-angular and round grains sand available in 50# and 100# bags, along with 4000# palletainers. Round Grain sand has a reduced surface area, significantly reducing the bon or binder needed in green sand and no-bake systems.

FAIRMOUNT MINERALS WEDRON SILICA:
CHROMITE
High-grade specialty sand occurs as magmatic segregations in ultrabasic igneous rocks that are mined and segregated. This sand is black in color and offers a very high heat transfer or a "chilling effect".
ZIRCON
110 AFS Florida mined, round shaped sand with high heat transfer.
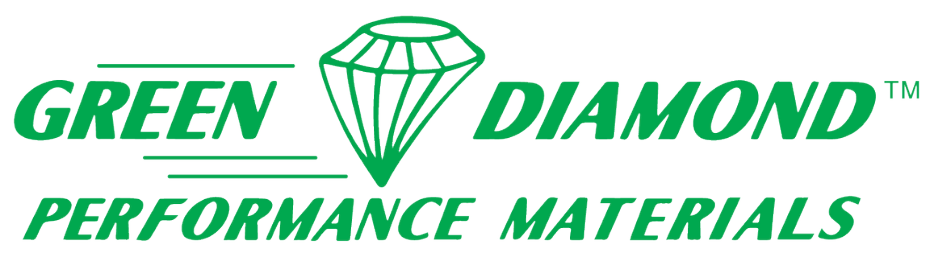
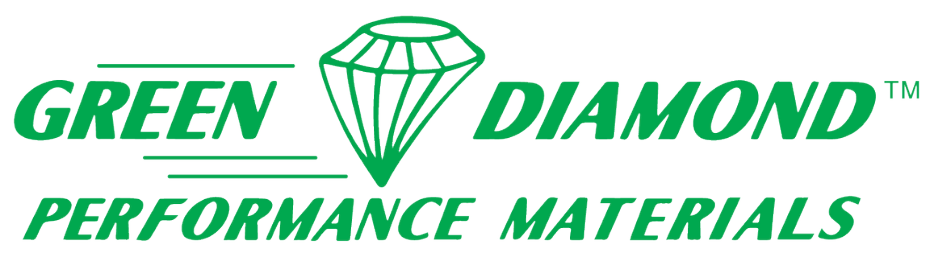
Green Diamond Sand
Molding Sand


About Green Diamond Sand
Green Diamond Performance Materials provides the foundry industry with a synthetic olivine sand produced in the United States containing no Free Silica. Our foundry material breaks down less than silica and natural olivine and comes with many advantages. The particle distribution of Green Diamond consistently meets American Foundry Society and Grain Fineness Number standards.
Adaptable for use with:
- Aluminum
- Brass
- Bronze
- Gray Iron
- Ductile Iron
- Manganese Steel
- Can also be used in green sand, no bake and lost foam applications, while providing clean, smooth, and consistent castings.
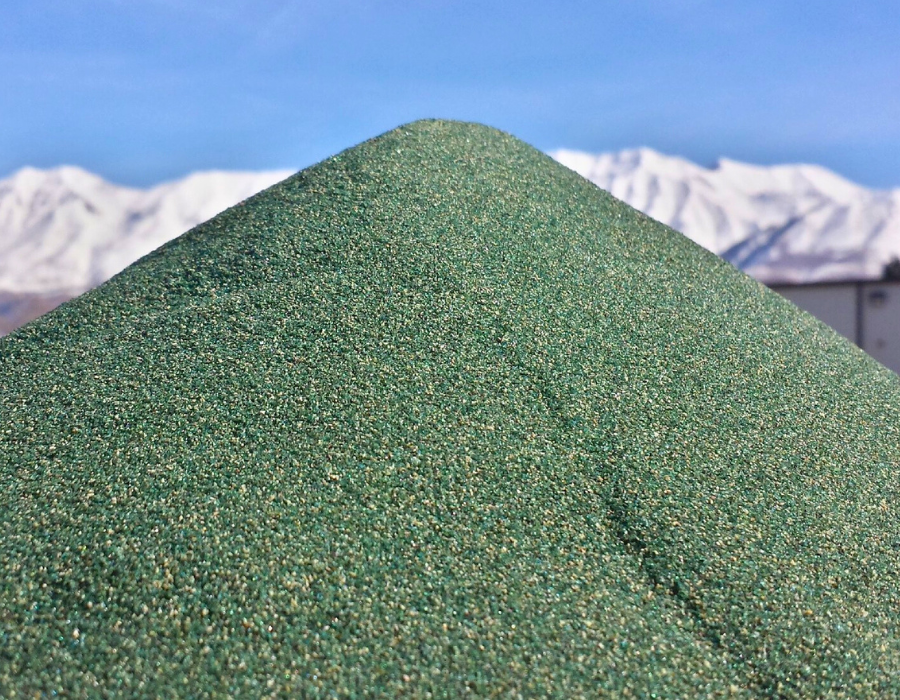
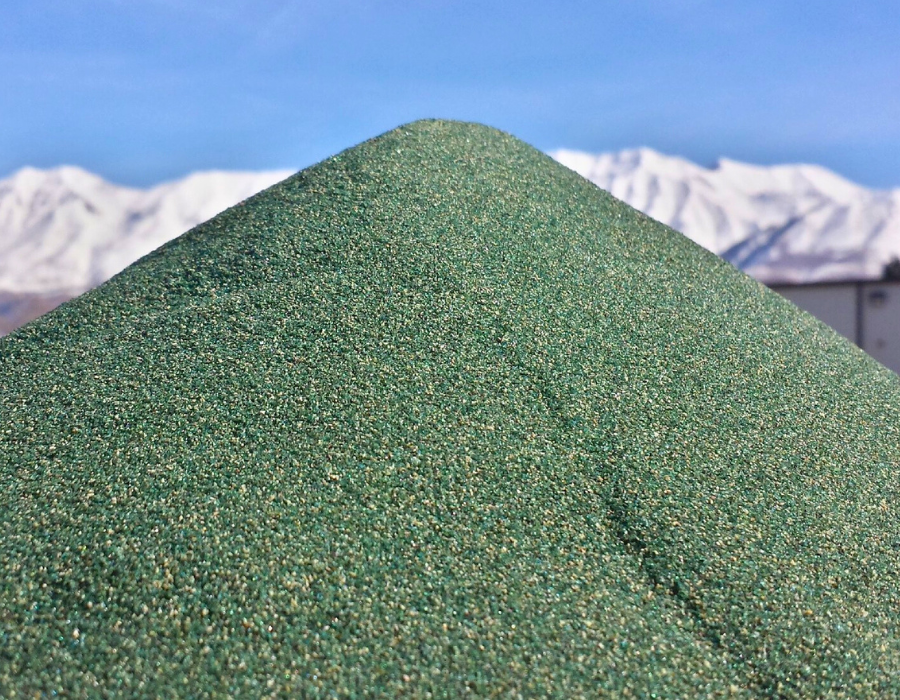
Green Diamond Sand is, by geological definition, synthetic olivine. Garnierite ore is melted and then granulated by quenching in fresh water. The quenching process renders granules devoid of crystalline structure, and therefore contain no free silica.
Advantages:
- Low thermal expansion reduces defects
- Low thermal conductivity decreases pouring temperatures by about 30-50°F
- Reduces make up sand additions and binder burnout
- No Loss On Ignition (LOI) eliminating pitting or gas defects
- Greater insulating values allows metal to flow up to 45% further than silica or olivine
- Can help reduce costs as you'll require less make up sand and binder additions while pouring less metal
Sand Additives
Sand additives are materials added to molding sand to enhance its performance and meet specific casting requirements. These additives modify the physical and chemical properties of the sand to improve casting quality, reduce defects, and ensure better mold performance.The choice of sand additives depends on the type of metal being cast, the casting process, and the specific requirements of the finished product.
VEINSEAL®
Veinseal® is a unique blend of superior quality materials specifically designed to improve your casting process. Technologically advanced formulations, intended for grey and ductile iron applications, actually controls the thermal expansion reaction of chemically bonded core sands without compromising core integrity; ultimately providing your process with defect-free castings and excellent surface finish!
Benefits:
- Save on machine labor and tool costs
- Prevent veining and gas defects
- Improve casting finish and process time
- Easy incorporation into your sand-core mix process
- No Loss On Ignition (LOI) with inorganic formulations
WESTERN BENTONITE (Sodium Montmorillonite)
One of the basic clays used in the metal casting industry.
Benefits:
- Offers the highest hot and dry strengths
- Develops a high degree of plasticity or toughness
- The best clay for hot sand
- Very high degree of durabilty
SOUTHERN BENTONITE (Calcium Montmorillonite)
Offers several characteristics different from western bentonite and is predominately used in nonferrous applications.
Benefits:
- Develops the highest green strengths
- Lowest hot and dry strengths
- Mulls faster and produces the most flowable sand
- Shakes-out freely
ADDITROL®
A single-package, custom additive blend of western and/or southern bentonites and organic additives, such as carbonaceous products, cereals, and starches. Additrol formulations can accommodate all green sand metal casting facilities, regardless of molding equipment, production rate, metal type or casting configuration. Additrol is blended to meet the needs of both ferrous and non-ferrous casting applications.
Benefits:
- Highest quality ingredients
- Accurately blended for individual applications
- Simplified material handling and inventory
- Single addition at muller minimizes process variables
- Eight conveniently located blending plants
- Variety of available raw materials to use for any application
SEACOAL
A highly volatile low ash, low sulphur bituminous coal ground to various degrees of fineness. When mixed with molding sand and contacted by a molten metal, the volatiles are released and give a quality to the casting called "peel". The sand does not stick to the casting, reducing cleaning cost and improving casting finish.
Benefits:
- Sand won't stick to the casting, reducing cleaning cost
- Improves casting finish, gives it "peel" quality