REFRACTORIES & COATINGS
Refractories are durable materials engineered to withstand extreme temperatures without breaking down, making them essential for lining furnaces, ladles, molds, and other equipment used in casting iron, steel, aluminum, and other alloys. They retain heat to maintain the proper temperature of molten metal and endure rapid heating and cooling cycles without cracking or degrading.
Explore
Some Of Our Most Popular Items
C-W 55 HS PLASTIC
Phos-bonded plastic designed to give excellent strengths, 58% Alumina.
ARMOR KOTE
Fine grained Graphitic veneering Mix for coating ladles, helps in the removal of slag build-up.
RAM MAX 60P SEAL
A fine grained phos-bonded veneering refractory, 60% Alumina. For use as a patch or lining material in molten metal handling equipment.
RAM MAX 80P SEAL
Veneering refractory, 85% Alumina, manufactured on the fine and wet consistent to be applied with a rubber glove or trowel to patch worn linings, spouts and other high wear areas.
90 RAM TR 90%
Veneering refractory, 85% Alumina, manufactured on the fine and wet consistent to be applied with a rubber glove or trowel to patch worn linings, spouts and other high wear areas.
90 RAM PC
Same and as 90 RAM TR, but a stiffer putty consistency. Works excellently for thin lining applications.
Cerecast 3000
High Alumina, low Iron castable that can be cast or gunned. It has excellent spalling and abrasion resistance as well as high strengths and volume stability.
We carry a large variety of products, contact us today to see if we have what you're looking for!
Core and Mold Coatings
Refractory coatings are applied to molds and cores to improve the surface finish of the castings and minimize defects that can occur at the sand-metal interface. These coatings provide a higher melting point than the sand and create an impermeable barrier between the sand grains and the molten metal.
The refractory system is the most critical coating component, directly determining the coating's overall effectiveness. The type, shape, size distribution, thermal expansion, chemical reactivity, thermal conductivity, and specific gravity are the basic criteria for the selection of the proper refractory.
Coatings developed by ASK Chemicals are far more than a pure barrier between sand and metal. They are high performance systems and determine in a decisive way the accuracy and surface quality of the casted parts and thus specifically eliminate typical casting defects. Whereas all coating systems are characterized by excellent casting results, low cleaning and fettling efforts as well as productivity and efficiency in the casting process, ASK Chemicals water-based coatings offer unbeatable advantages.
The Coatings available are based on
5 major components:
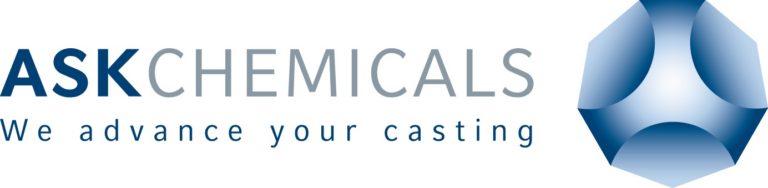
- REFRACTORY SYSTEM
- CARRIER SYSTEM
- SUSPENSION SYSTEM
- BINDER SYSTEM
- CHEMICAL MODIFIERS
Benefits:
- Storage volumes are unlimited
- Adjusted processing characteristics
- No further expenses for dilution (solvents)
- Improved casting surfaces
- No pollution and contamination danger for employees by solvents
- No need of further safety measures concerning fire protection
- Emission-free
- Deliver excellent casting results
- Low cleaning and fettling efforts
- Increase productivity and efficiency in the pouring process
- No need of installation of explosion hazardous equipment
- Produce significantly more convincing casting results than conventional coatings